2022 Trends In Industrial Automation
Predictive Maintenance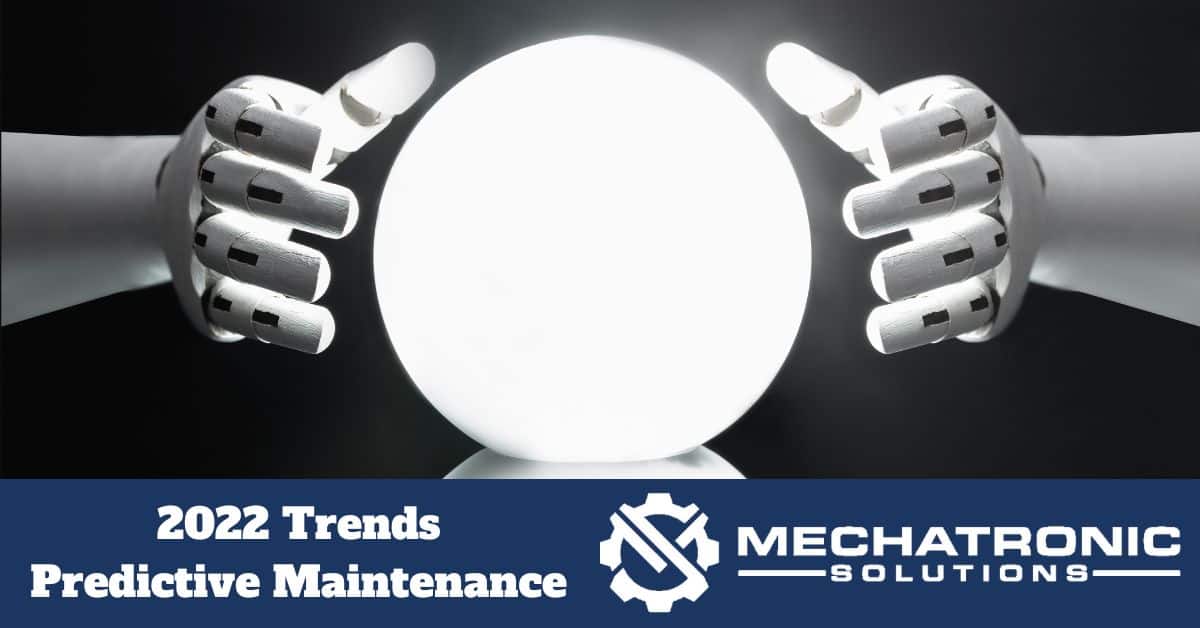
Predictive maintenance is a proactive condition-based maintenance strategy that remotely monitors the condition of equipment using Industrial Internet of Things (IIoT) sensor devices.
The IIoT devices supply real-time data of equipment, and analytics are performed to predict when equipment requires maintenance. Predictive maintenance is aimed at reducing costly, unexpected breakdowns, and offers the manufacturer the opportunity to plan the maintenance around their production schedule.
Manufacturing Industry Challenges Prompting Predictive Maintenance
Unplanned Downtime
One of the major challenges faced by manufacturers is unplanned downtime. Unplanned downtime refers to when there is an unexpected shutdown or failure of equipment or a process. 82% of companies reported experiencing unplanned downtime. This causes costly delays in maintenance, production, and deliveries. It can cost some companies up to $260,000/hour of downtime, and recent studies also show the problem costs manufacturers a total of $50 billion each year.
High Maintenance Costs
Another major challenge faced at manufacturing plants is high maintenance costs. As equipment, machines and plant infrastructure in general ages, repairs become more frequent and the cost of maintenance increases. On average, maintenance workers spend 19 hours/week on scheduled maintenance so they can reduce the chances of unplanned downtime.
Shortage of Maintenance Workers
Lastly, many plants are being hit hard by a shortage of maintenance workers which is impacting their ability to maintain optimal production levels. This skilled labor gap is being exacerbated by the fact that many experienced plant maintenance workers are retiring or approaching retirement and manufacturers are struggling to fill these roles with younger talent. The COVID-19 pandemic has also made the situation worse as plants may be limited or without maintenance workers if staff gets sick.
The Evolution of Maintenance Strategies
Maintenance practices have drastically evolved as manufacturing plants and systems have become more complex. The graphic below illustrates the evolution of the top maintenance strategies deployed by manufacturing companies over recent years:
Predictive Maintenance Solutions
Omron’s predictive maintenance solutions allow multiple pieces of equipment to be monitored simultaneously using EtherNet/IP and Modbus TCP communication. Below, we outline a few of these solutions.
S8VK-X Power Supply
Omron’s S8VK-X power supplies have an Ethernet port that allows them to be connected and remotely monitored anywhere connected to the internet. It allows you to monitor the internal status of the power supply, showing voltage output, current output, peak current output, years until replacement and total run time, while allowing the user to set alerts to the status of any of these conditions. The remote monitoring software is included. Below is an example monitoring screen with conditions and history graphic:
K6CM Motor Condition Monitoring Devices
Omron’s K6CM product line includes 3 different products designed to monitor wear conditions associated with 3-phase motors. The K6CM-VBM measures temperature and vibration associated with bearing wear. The K6CM-CI measures current abnormalities associated with debris and pump cavitation. The K6CM-ISM measures insulation resistance associated with insulation breakdown inside of a 3-phase motor.
The K6CM monitoring tool allows you to monitor all your motors with one simple software. Frequent manual motor inspections are no longer needed because real-time alerts of abnormalities notify you when maintenance is needed.
K6PM Thermal Condition Monitor
Omron’s K6PM Thermal Condition Monitor solution consists of a thermal infrared sensor and a controller with EtherNet/IP and Modbus TCP communication. It offers continuous thermal monitoring of critical components such as high voltage control panels, transformers, gearboxes, and more. The sensor’s wide viewing angle and compact body allows for flexible installations. The DIN-rail mount controller features an alarm bar and LCD display, and 31 sensors can be used per controller.
This solution eliminates the need for manual thermal inspections and allows the user to monitor these components in real-time via the free PC monitoring software.
Steps to Integrate Predictive Maintenance Devices into Existing Equipment
Integrating predictive maintenance solutions into existing equipment can seem like a daunting task, but Omron’s products are designed to be retrofitted to existing equipment. Following these six steps will help you integrate predictive maintenance devices into your existing equipment:
Contact Mechatronic Solutions
Mechatronic Solutions is a leading distributor of Omron’s industrial automation products, including their predictive maintenance solutions, for Minnesota, Wisconsin, North Dakota, and South Dakota. If you would like more information or have any questions, please fill out our contact form and a member of our team will reach out to you.
PRODUCTS
PRODUCTS
MANUFACTURERS
AUTOMATION SOLUTIONS
INFO CENTER
ABOUT US
SCHEDULE A
DEMO